Reliable Ammonia Catalyst Solution
Methanol Plant
SYAMCAT Primary steam-reforming catalyst is a new set of nickel based catalyst designed for oil field gas steam reforming applications.
It's suitable for steam reforming hydrogen production devices that use oil field gas or natural gas as feedstocks to produce industrial hydrogen, ammonia synthesis gas, methanol synthesis gas, and metallurgical reduction gas.
It's also suitable for It is a modern energy-saving AMV or Braun low water to carbon ratio conversion ammonia synthesis gas process.
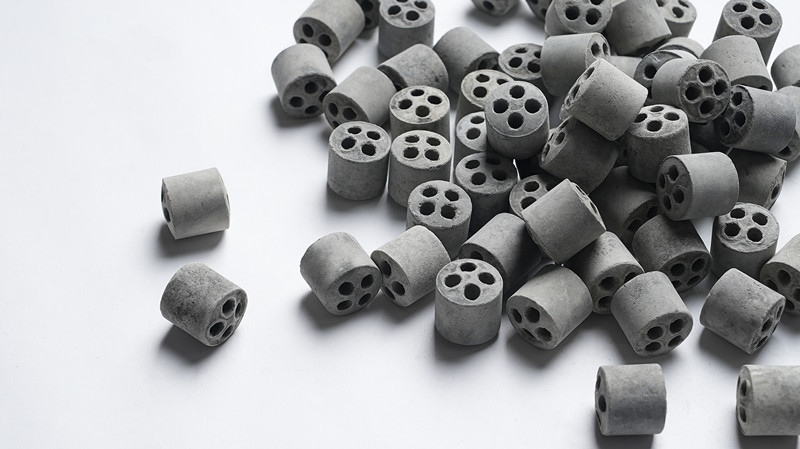
Why Choose SYAMCAT Primary Steam Reforming Catalyst?
≥12%
More than 12% active components Nickel Oxide are added.
Excellent Reducibility
Through self- circulation reduction, natural gas feedstock can be directly introduced into the reformer without extra activation in advance.
5+
5+ years of high guaranteed service life
Production Process of SYAMCAT Primary Steam Reforming Catalyst
① Active Component Preparation: Nickel nitrate, the active component compound, is precisely prepared for optimal effectiveness.
② Catalyst Carrier and Additive Incorporation: Al₂O₃, serving as the carrier, is mixed with suitable additives to enhance performance.
② Catalyst Carrier and Additive Incorporation: Al₂O₃, serving as the carrier, is mixed with suitable additives to enhance performance.
③ Co-precipitation: The raw materials are combined with an acidic solution, initiating co-precipitation reaction and aging to form the catalyst base.
④ Washing and Drying: After the reaction, the precipitate is thoroughly washed, dried, dehydrated, and decomposed for stability.
⑤ Grinding and Sieving: The resulting catalyst material is ball-milled to achieve a fine consistency, passing through a 120-mesh sieve at a 90% rate.
⑥ Homogeneous Mixing and Pelletization: The grinding material is moistened, ensuring homogeneity, and then pelletized for consistent form.
⑦ Compression molding: The pellets are pressed into the desired shape, optimizing the catalyst's efficiency and readiness for application.
④ Washing and Drying: After the reaction, the precipitate is thoroughly washed, dried, dehydrated, and decomposed for stability.
⑤ Grinding and Sieving: The resulting catalyst material is ball-milled to achieve a fine consistency, passing through a 120-mesh sieve at a 90% rate.
⑥ Homogeneous Mixing and Pelletization: The grinding material is moistened, ensuring homogeneity, and then pelletized for consistent form.
⑦ Compression molding: The pellets are pressed into the desired shape, optimizing the catalyst's efficiency and readiness for application.
Primary steam reforming catalyst production process flow chart:
Mixing → Co-precipitation, aging→Washing →Dehydration and drying→Grinding and sieving→Wet mixing→Grinding→Granulation→Compression molding
SYAMCAT Primary Steam Reforming Catalyst Solution
The stable performance of the primary reforming catalyst is the basic requirement for the supplier of the synthetic ammonia plant. It is an important factor in the service life of the catalyst, and it is also a part that SYAMCAT pays special attention to.
Therefore, we strictly control the performance of the catalyst from the preparation process of primary reformer catalyst.
Paying attention to the order of adding the catalyst components has a certain influence on the carbon deposition performance of the catalyst; Choosing a more suitable preparation method has a great impact on the dispersion of catalyst active components; Adding suitable catalyst additives will make the catalyst own stable activity; Increasing the surface alkalinity of the carrier will enhance the ability of the catalyst surface to absorb water vapor and CO2; Paying attention to the choice of shape will affect the activity, strength, resistance and heat transfer performance of the primary reforming catalyst.
6 products found
ViewList
Model: SYAMCAT YZ119/SYAMCAT YZ119R
Pre-reforming catalyst is a high Ni system supported on a porous carrier.
FavoritesModel: SYAMCAT Z433/SYAMCAT Z434
Enhance your ammonia synthesis gas production with SYAMCAT's Primary Steam Reforming Catalyst.
FavoritesModel: SYAMCAT XT317/SYAMCAT XT318
ZnO Desulfuration Catalyst has deep desulfurization extent, easy to use and high sulfur capacity.
FavoritesModel: SYAMCAT YJ17/SYAMCAT YJ18/SYAMCAT YJ19
Hydrogenation catalyst for hydrogen production with cobalt molybdenum nickel ternary active components.
FavoritesModel: SYAMCAT HJ323
Methanol synthesis catalyst with alumina as carrier and copper as active component.
FavoritesModel: SYAMCAT Z428Q/SYAMCAT Z429Q
Elevate your ammonia plant's efficiency with SYAMCAT's Primary Steam Reforming Catalyst.
FavoritesSYAMCAT's Technology Service of Primary Steam Reforming Catalyst

Customized Catalyst Solutions:
The professional technical team will optimize the primary steam reforming catalyst according to your operating conditions/requests and propose the most suitable product to you.

Guaranteed 5-Year Service Life:
An official authoritative guarantee of a service life of at least 5 years;

Expert Remote Guidance and Technical Support:
Remote guidance and technical services for catalyst start-up, loading, maintenance of any in-service shutdown, etc. If on-site instruction is required, a small fee will be charged according to the time.

Real-Time Production Monitoring and Support:
Monitor and record data for your production operations at any time (your cooperation is required), and provide real-time technical advice or parameter adjustments if necessary for various conditions during operation.
FAQs of SYAMCAT Primary Steam Reforming Catalyst
- Q:
- What are the industries in which primary steam reforming catalyst are used?
- A:
- The catalyst is suitable for the reaction of hydrocarbons with water to H₂, CO, CO₂ in the reforming section of ammonia, methanol or hydrogen plants made from different raw materials, such as natural gas, coke oven gas, refinery gas, naphtha, associated gas from oil fields, etc. The catalyst is also suitable for the reaction of ammonia cracking to hydrogen plant. It is also suitable for ammonia cracking to hydrogen plant.
- Q:
- Does the shape of the primary steam reforming catalyst have an effect on the performance?
- A:
- Vapour reforming of natural gas on the catalyst surface at high temperatures is very fast, the reaction process is controlled by internal diffusion, and the apparent activity increases significantly with increasing catalyst geometry. The apparent activity of the small particle size catalyst increases due to the increased geometric surface and improved heat transfer in the tube, but its resistance also increases. The shape also affects the activity, strength, resistance and heat transfer properties of the catalysts. SYAMCAT's primary reforming catalyst is a four-hole convex cylindrical honeycomb type, which is characterised by a large outer surface, high void fraction, reduced resistance and uniform airflow distribution.
- Q:
- Do you handle nickel based catalysts?
- A:
- Our nickel based catalysts are meticulously designed to meet the demands of diverse industrial processes. Whether you require catalysts for hydrogenation, hydrogen production, or environmental applications in coking furnaces, SYAMCAT has you covered. With a focus on efficiency and sustainability, our catalysts deliver optimal performance, ensuring smooth operations and minimizing environmental impact.
- Q:
- How often should the performance of steam reforming nickel catalysts be monitored?
- A:
- Regular monitoring of steam reforming nickel catalysts is crucial for optimal performance. It should be done periodically, ranging from weekly to monthly intervals, depending on operating conditions and catalyst lifespan. Monitoring helps detect deviations from expected performance, allowing timely adjustments to maintain efficiency. It also identifies issues like catalyst degradation or fouling, optimizing usage and minimizing downtime.
Please send your message to us
SYAMCAT is a professional manufacturer of synthetic ammonia catalysts with over 30 years of catalyst experience and history,Through continuous technological innovation, we offer catalyst solutions for ammonia production.If you would like to learn more or are in search of a manufacturer for synthetic ammonia catalysts for your company, please feel free to contact us.
- Tel
- *Title
- *Content
subscription