Strategies for Alleviating Sulfur Poisoning in Methane Steam Reforming Catalysts
Strategies for Alleviating Sulfur Poisoning in Methane Steam Reforming Catalysts
Feedstock derived from natural gas often contains sulfur compounds such as hydrogen sulfide (H2S), sulfur dioxide (SO2), carbon disulfide (CS2), mercaptans, and thiophenes if not subjected to thorough desulfurization treatment. In methane steam reforming, H2S emerges as the primary sulfur compound, with different sulfur compounds causing catalyst poisoning via distinct pathways. Throughout the reforming process, the generation of high-temperature water vapor or hydrogen prompts the conversion of most sulfur compounds to H2S, which subsequently adsorbs onto active sites, resulting in catalyst poisoning. Thus, H2S stands as the main culprit, triggering deactivation mechanisms like sulfidation of active components and accelerated carbon deposition.
Methods for Mitigating Sulfur Poisoning in Methane Steam Reforming Catalysts
Noble Metal Catalysts
Researchers like Fumihiro have explored the use of noble metals such as Rh, Pt, Ir, and Ru as active components in methane steam reforming catalysts. Experiments utilizing methane with dimethyl sulfide as a feedstock for steam reforming revealed robust sulfur resistance in Pt and Ir catalysts. These catalysts completely regenerated from sulfur poisoning, achieving regeneration rates comparable to initial conversion rates. Noble metals can serve as alternatives to transition metal Nickel in reforming reactions, offering similar catalytic performance with higher sulfur resistance. However, the high cost of noble metals hampers their widespread application.
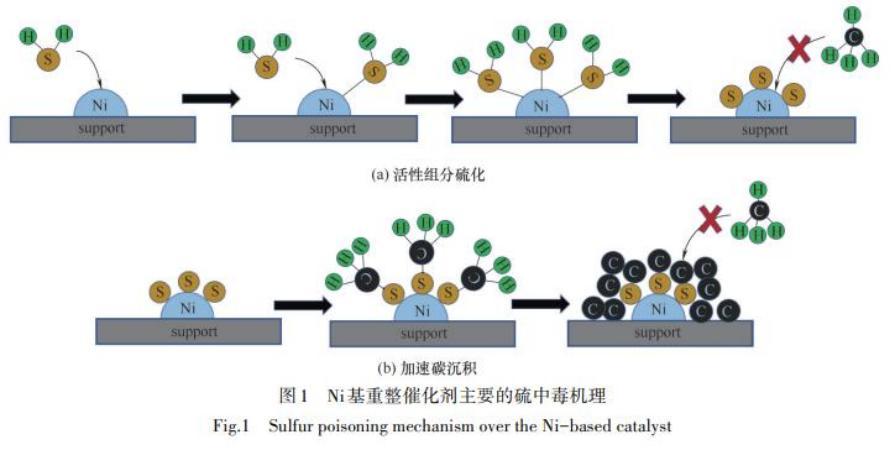
Bimetallic and Multimetallic Catalysts
An alternative approach entails incorporating sulfur-resistant elements into Nickel catalysts, including noble metals like Pt, Pd, Au, and transition metals like Mo. This addition modifies the microelectronic environment and structure of Ni-based catalysts, suppressing sulfur adsorption on active components or acting as sacrificial agents to mitigate sulfur's impact on active sites, thereby enhancing sulfur resistance. Studies by Kantserova on methane tri-reforming catalysts loaded with Ni-Cu, Ni-Pt, and Ni-Pd on CeO2 demonstrated superior sulfur resistance in Ni-Pt and Ni-Pd catalysts compared to Ni-Cu catalysts.
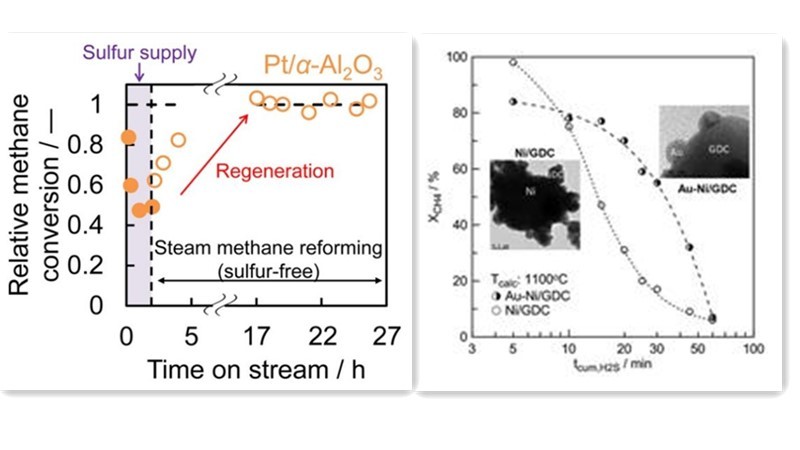
Catalyst Carrier and Other Approaches:
Researchers like Chen Xi have explored novel carrier materials such as alumina-activated carbon composite (AAC) for loading Nickel based catalysts, showcasing significantly improved sulfur resistance compared to Ni/Al2O3 in methane steam reforming experiments containing H2S. Additionally, studies by Postole on the interaction between sulfur compounds and commercial Ce0.9Gd0.1O2 carriers in methane steam reforming revealed that sulfur adsorption on the surface could replace oxygen vacancies on CeO2, disrupting crystal structures and generating new catalytic sites, thereby enhancing catalytic activity.
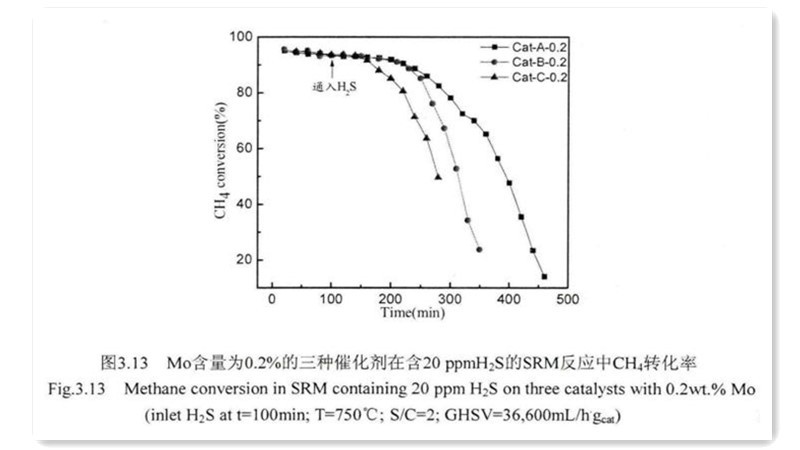
Discover Customized Solutions with SYAMCAT
At SYAMCAT, we understand the complexity of sulfur poisoning in methane steam reforming catalysts and offer tailored solutions to address your specific challenges. Our team of experts is committed to providing innovative catalyst solutions for ammonia plants, leveraging cutting-edge research and technology to optimize performance and efficiency. Contact us today to explore customized solutions tailored to your unique needs and propel your operations to new heights of success.
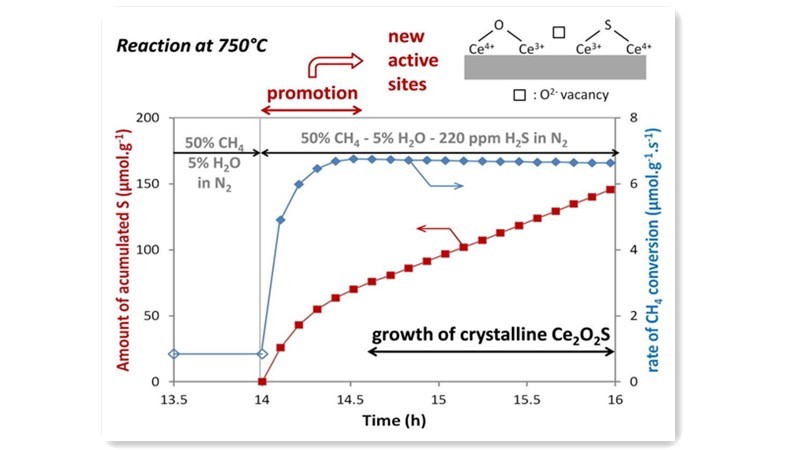