Impact of Chlorine on Steam Reforming Catalysts in Hydrocarbon Conversion for Hydrogen Production
Impact of Chlorine on Steam Reforming Catalysts in Hydrocarbon Conversion for Hydrogen Production
Chlorine present in the feedstock not only causes corrosion to the equipment and pipelines of the hydrogen production unit, leading to issues like stress cracking, but also poisons the catalyst to varying degrees.
Sources of Chlorine
Chlorine is one of the main poisons for nickel-based steam reforming catalysts. During industrial operations, chlorine can enter the system through various pathways: as a component of the hydrogen-producing feedstock itself, through ineffective purification and dechlorination systems, from unqualified boiler feedwater containing chlorine, via contaminated external steam, and through other process streams tainted with chlorine.
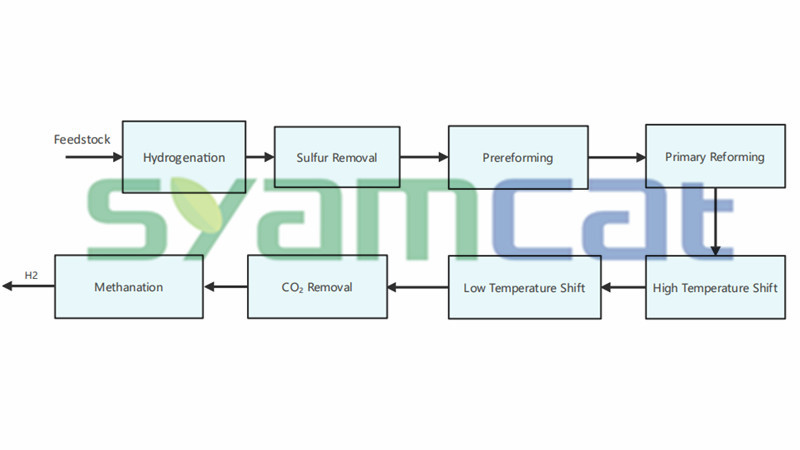
Harmful Effects of Chlorine on Steam Reforming Catalysts
Hydrogen chloride reacts with zinc oxide desulfurizers to form zinc chloride, which melts at 285°C. At operating temperatures, molten zinc chloride covers the surface of the desulfurizer, preventing H2S from entering the desulfuizer's surface layer and significantly reducing desulfurization performance, accelerating catalyst aging. Additionally, hydrogen chloride accelerates the loss of the anti-carbon component K2O in conversion catalysts, leading to a decrease in carbon resistance. Chlorine not only adsorbs on the upper catalyst bed but also migrates downward through material flow, causing harm to lower catalysts, resulting in poisoning and deactivation of the entire bed. While chlorine-induced catalyst poisoning is reversible, its impact is more severe than sulfur. A large amount of chlorine entering the bed promotes catalyst sintering, resulting in permanent poisoning and catalyst failure. If the catalyst contains Na2O (from boiler water) or K2O (from steam reforming catalysts and refractory materials), it reacts with chloride to form NaCl and KCl, covering the outer surface of the catalyst particles, blocking most of the surface channels, and dramatically reducing catalyst activity.
Chlorine Poisoning and Catalyst Regeneration
Although chlorine poisoning of catalysts is reversible, regeneration is challenging and typically involves a steam atmosphere. Regeneration is conducted by cutting off hydrocarbon feeds, maintaining steam at approximately 30% of full load, and operating at the original conversion temperature, which can maintain the original pressure or reduce it. During steam regeneration, the reduced state of the conversion catalyst is oxidized, necessitating re-reduction after regeneration, which is usually combined with desulfurization.
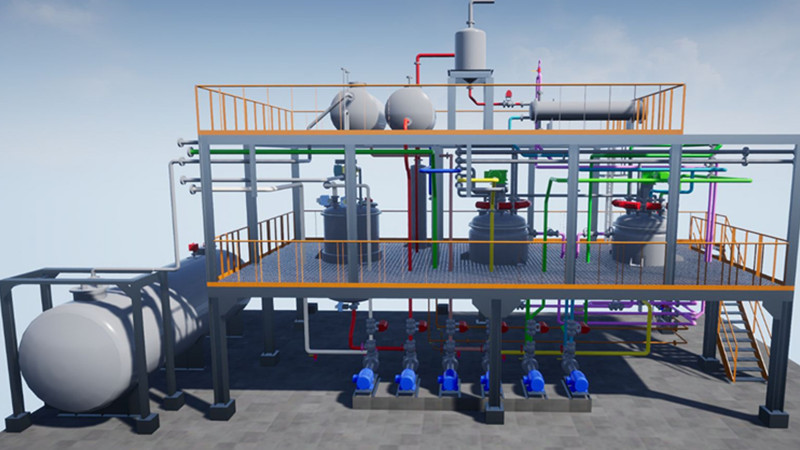
Anomalies Caused by Chlorine Poisoning in Steam Reforming Systems
Chlorine entering the conversion system leads to a decline in catalyst activity. Symptoms include redness in the upper furnace tubes, followed by the entire furnace, an increase in bed temperature, and methane residual at the reforming outlet. In severe cases, the presence of high hydrocarbons, especially aromatics, can penetrate the conversion bed, causing catalyst failure and preventing heavy hydrocarbon cracking and conversion, resulting in carbon deposition on the catalyst.
Prevention of Chlorine Poisoning
To safeguard against chlorine poisoning of catalysts, stringent measures must be implemented to ensure feed purification and steam quality control. Employing high-efficiency dechlorination agents in the feed purification and dechlorination system is paramount to achieving dechlorination accuracy below 0.5 * 10-6, preferably below 0.2 * 10-6. It is crucial to closely monitor chlorine content in boiler feedwater and maintain it within strict limits. Additionally, incorporating secondary desalinated water into the process steam supply guarantees that the chlorine content remains consistently below 0.1 * 10-6, safeguarding the integrity and performance of steam reforming catalysts.
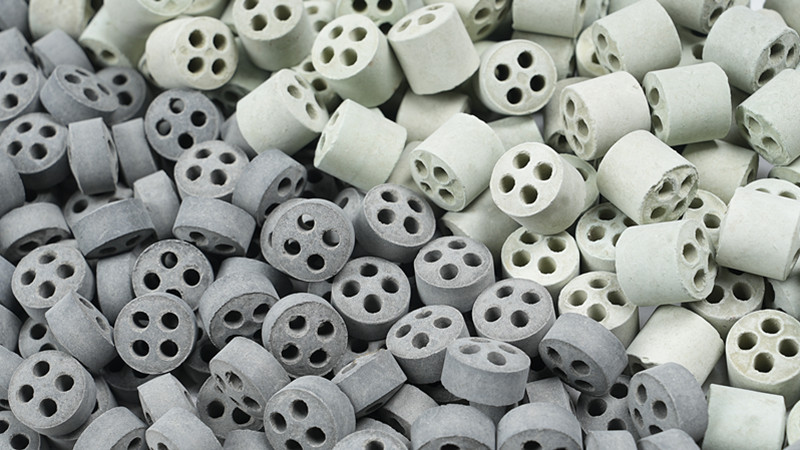
For expert guidance on mitigating chlorine-induced catalyst poisoning and optimizing hydrogen production processes, rely on SYAMCAT's seasoned team of catalyst specialists. Our experts possess a wealth of experience in tackling chlorine-related challenges and are equipped with innovative solutions tailored to your specific hydreogen production needs. Contact us today to embark on a journey towards unlocking the full potential of your hydrogen production operations, and let SYAMCAT be your trusted partner in catalyzing success.