Exploring the Frontier of Methane Steam Reforming Catalyst Development
Exploring the Frontier of Methane Steam Reforming Catalyst Development
In ammonia synthesis, various methods exist for the steam reforming stage, classified according to feedstocks: natural gas, coke, and heavy oil. Among them, steam methane reforming (SMR) in natural gas hydrogen production is the most established hydrogen production technology globally, constituting roughly 70% of global hydrogen production. Therefore, natural gas is the mainstream feedstock for synthesizing ammonia.
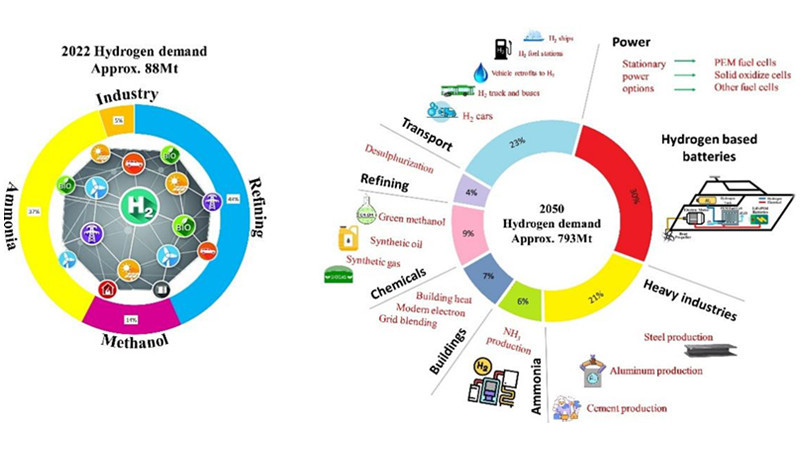
Milestone Moments: A Historical Overview of Methane Steam Reforming
Since the industrial application of methane steam reforming by the German BASF Group in 1926, researchers have continually enhanced this process and catalysts. Presently, it stands as one of the most mature processes for hydrogen and synthesis gas production, crucial for ammonia synthesis. The main process flows include the Kellogg process in the United States, the Braun process, and the ICI-AMV process by the British Imperial Chemical Industries.
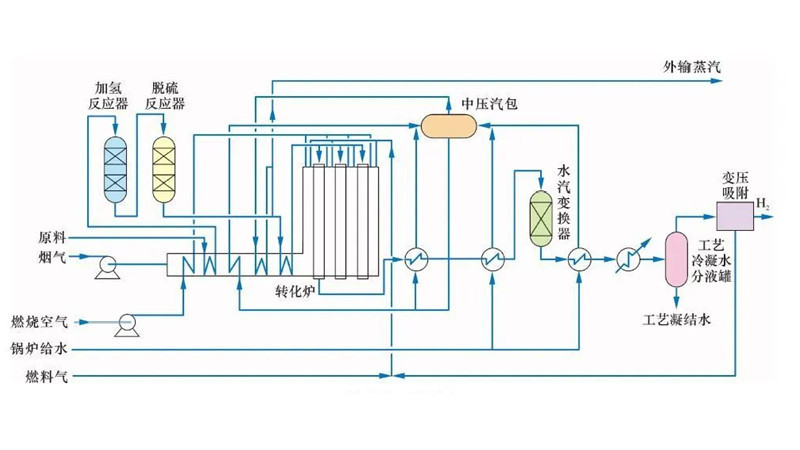
Driving Efficiency: The Role of Nickel-Based Catalysts in Methane Conversion
Methane steam reforming is an endothermic process, typically employing nickel-based catalysts to boost methane conversion and mitigate catalyst coking. Typically, reaction temperatures range from 750 to 920°C, with an inlet H2O/CH4 ratio of 2.0 to 6.0 (molar ratio). Steam Reforming Catalysts may incorporate alkaline oxides or rare earth metal oxides as promoters to improve performance.
Unveiling Catalytic Mechanisms: Insights from Methane Sulfur Reforming Studies
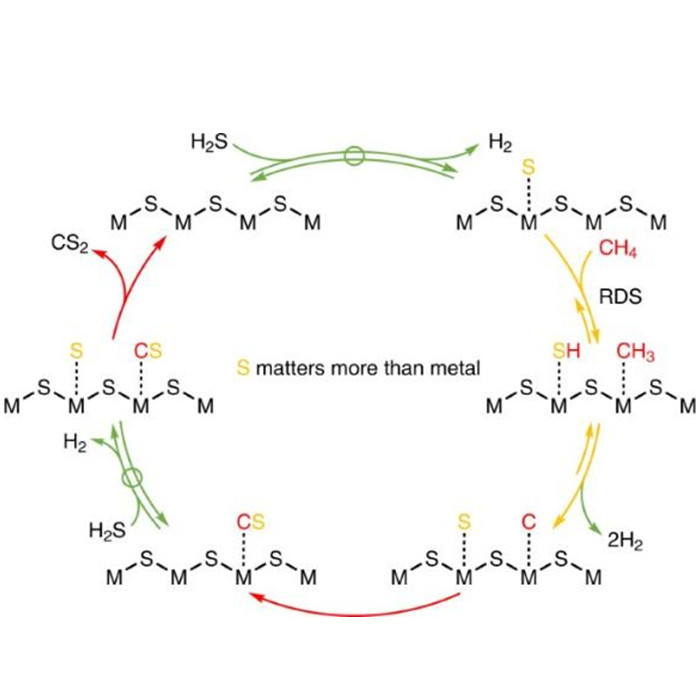
The research group led by Shihui Shi at Yangzhou University conducted a systematic study on the catalytic system and intrinsic activity of methane sulfur reforming reaction. Their findings, based on kinetics and isotope exchange studies, suggest that the hydrogen generation and hydrogen sulfide decomposition processes are reversible and balanced. The combination of surface carbon and sulfur species is quasi-irreversible, while the first step of methane's carbon-hydrogen bond dissociation, although reversible, is far from equilibrium and considered the rate-determining step. Furthermore, they discovered a unique and universal surface reaction mechanism on transition metal oxides and sulfides, namely the mechanism of methane carbon-hydrogen bond activation catalyzed by dynamically formed low-coordinated surface S* species. This provides a theoretical basis for designing more efficient catalytic systems and offers insights into the desulfurization process prior to conversion.
Harnessing Redox Reactions: Carbon Dioxide Utilization in Methane Reforming
Galvita and Marin at Ghent University in Belgium employed Nickel catalysts, CaO/Al2O3, and Fe3O4/MgAl2O4 as three types of catalysts. Through the process of redox reactions, they separated hydrogen-containing species from carbon-containing species, shifting the equilibrium and increasing the conversion rate of carbon dioxide, ultimately obtaining products rich in carbon monoxide. This has led to the development of a new methane super-dry reforming process. In the methane reforming process, CaO stores carbon dioxide and separates water, greatly reducing the water-gas shift reaction. Additionally, Fe3O4 temporarily stores "reducing agents," achieving high selectivity in carbon monoxide production. Moreover, CaO storage of carbon dioxide allows for the use of methane products with higher CO2 content (such as biogas) as feedstock, further reducing reaction costs.
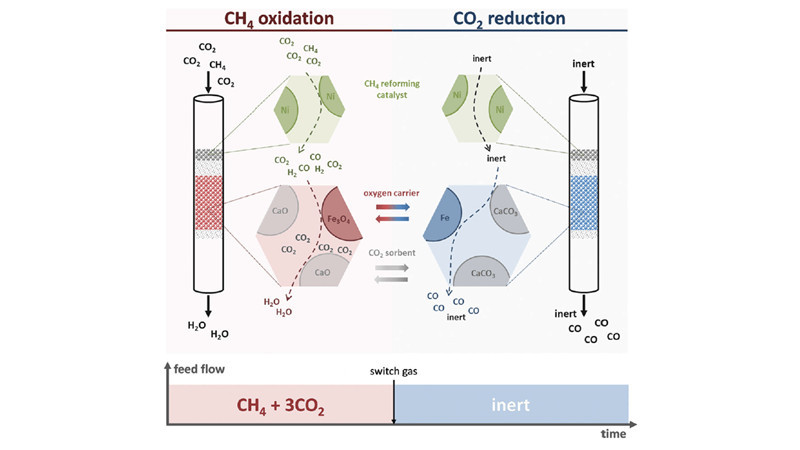
Innovative Synthesis Techniques: Sol-Gel Method for Mesoporous Alumina Catalysts
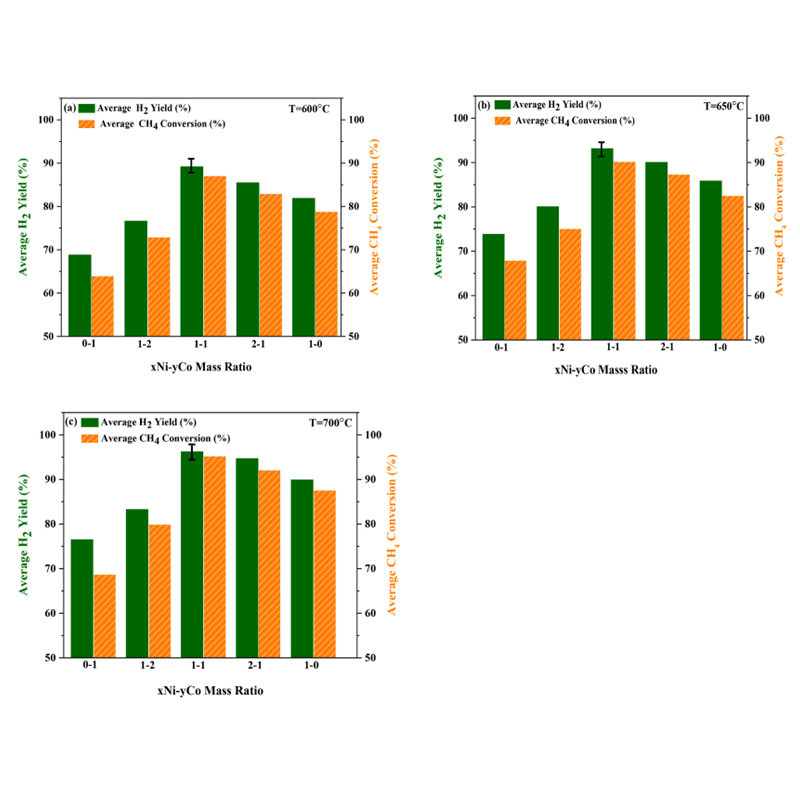
Sara Zolghadri at Azad University in Iran utilized a sol-gel self-assembly method to synthesize mesoporous alumina. They studied the effects of different Ni/Co mass ratios on methane steam reforming (SRM). The 10Ni10Co catalyst with a high specific surface area (249.91 m2/g) exhibited the highest methane conversion rate and H2 yield (95.7% and 96.2%, respectively) and the lowest carbon deposition (3.6%), attributed to the highly dispersed active centers and synergistic effects of Ni and Co particles.
Enhanced Coking Resistance: Nickel-Cobalt Alloy Catalysts for Methane Steam Reforming
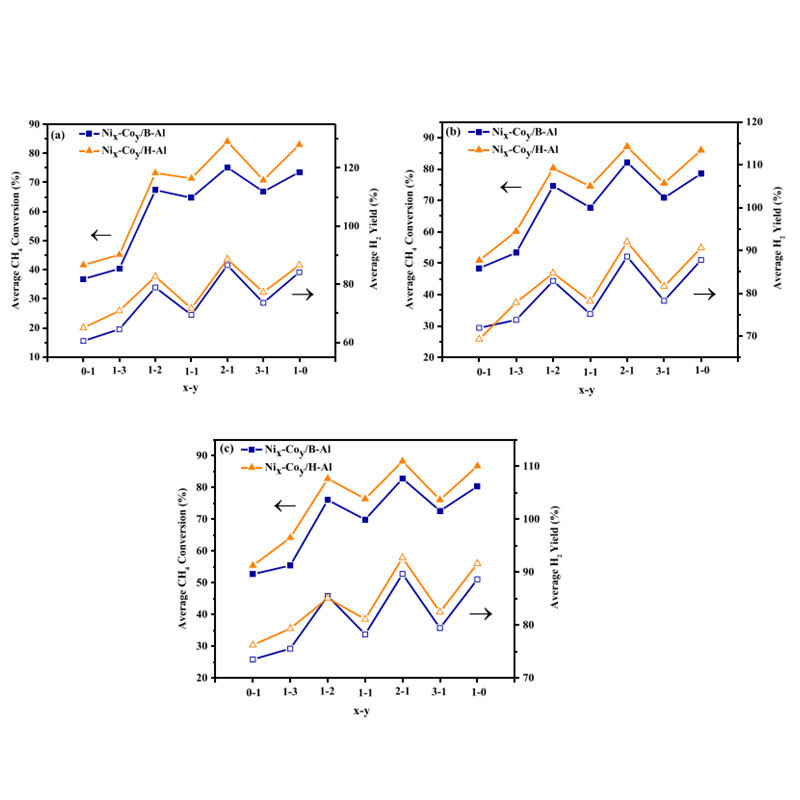
Fateme at Shiraz University reported on the effects of Co addition to Ni/Al2O3 catalysts. They synthesized Ni/Co loaded on solid or hollow sphere Al2O3 with various mass ratios and studied their activity and stability in coking formation. Among the prepared catalysts, Ni2-Co1/H-Al2O3 showed the highest activity, with methane conversion rate of 88.2% at 700°C and hydrogen yield of 92.7%. Furthermore, their research results indicated that Co can enhance coking resistance and suppress the activity of low-coordinated nickel sites.
Optimizing Catalytic Formulations: The Role of Fe/Ni Ratio in Modified Calcite Catalysts
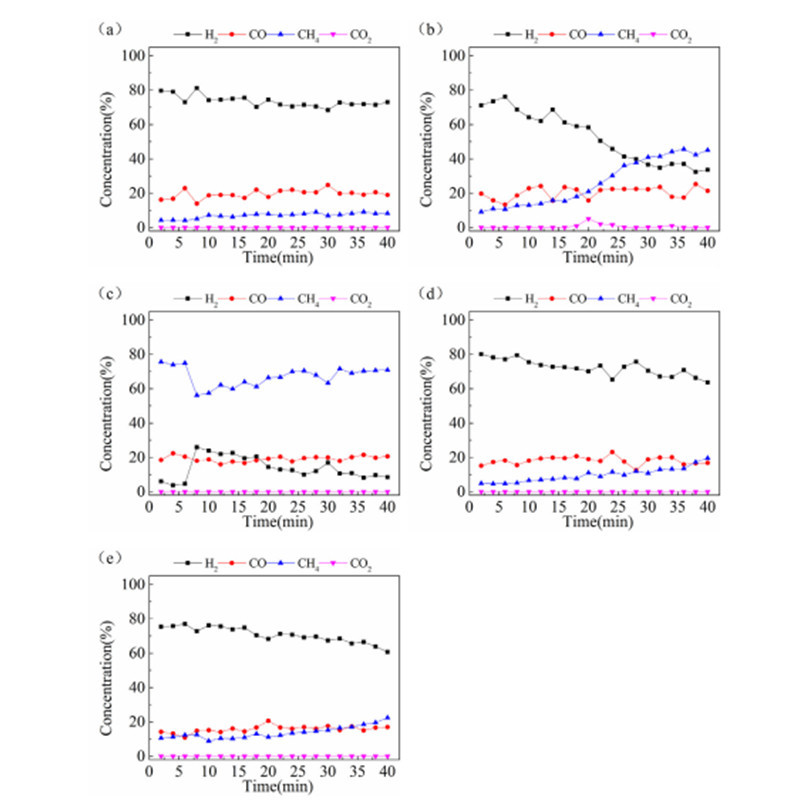
Zhi Feng Hu et al. at South China Agricultural University prepared Ni-Fe modified calcite catalysts for methane steam reforming. The results showed that the Fe/Ni ratio of 0.67 was the optimal choice for the process, while excessive iron loading led to catalyst sintering. The material exhibited excellent catalytic activity, with methane conversion rate of 98.9% and hydrogen yield of 93.8% at 800°C.
Revolutionizing Industrial Processes: Syamcat Steam Reforming Catalysts
At the forefront of methane steam reforming catalysts, Syamcat offers cutting-edge solutions designed to optimize industrial processes. Our Syamcat steam reforming catalyst is engineered with advanced technology to deliver superior performance and efficiency. By leveraging our catalysts, industries can experience enhanced methane conversion rates, improved hydrogen yields, and reduced carbon deposition, leading to increased productivity and cost savings.
Experience the Syamcat Advantage: Consultation and Support for Your Catalyst Needs
We invite you to explore the benefits of Syamcat steam reforming catalyst for your specific applications. Our team of experts is available to provide personalized consultations and support to help you achieve exceptional results. Contact us today to learn more about how Syamcat catalysts can revolutionize your methane steam reforming processes.
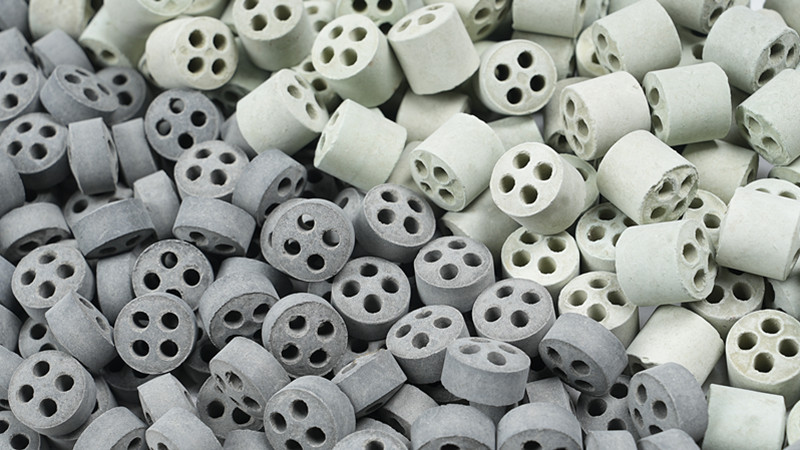