Maximizing Efficiency in Steam Reforming Catalyst Management: Best Practices and Innovations
Maximizing Efficiency in Steam Reforming Catalyst Management: Best Practices and Innovations
To combat steam reforming catalyst deactivation stemming from excessive oxidation and nickel loss, various measures can be employed:
Principle of Steam Reforming Catalyst Deactivation
During the shutdown of an ammonia synthesis plant, water vapor forms a protective film on the catalyst surface, inhibiting further nickel oxidation. Nickel reacts with water vapor as follows:
Ni+H2O=NiO+H2+2.56KJ/mol
This reaction, being minimally exothermic, lowers the risk of overheating. Thus, steam is commonly used as the oxidizing agent for catalyst heating and passivation in most ammonia plants.
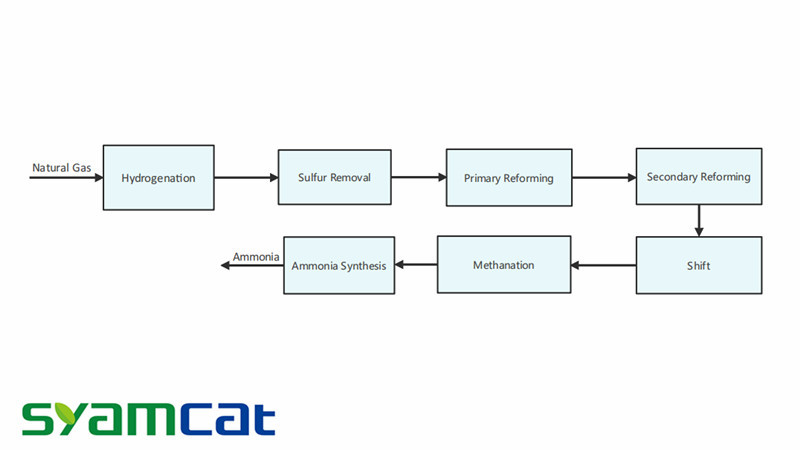
Impact of Water Vapor on Steam Reforming Catalyst
Utilizing water vapor for catalyst oxidation leads to reduced pore volume, significant pore enlargement, and a rapid decline in specific surface area, resulting in decreased catalyst activity. Prolonged exposure to high-temperature water vapor can form inactive nickel aluminate spinel (NiAl2O4) through interaction between NiO and Al2O3, leading to micropore obliteration and catalyst deactivation. Additionally, substantial water vapor can enhance gas flow rate within catalyst pores, promoting uniform gas distribution in reformer tubes. Consequently, industrial applications predominantly use a steam and natural gas mixture as the primary activation medium for reforming catalysts.
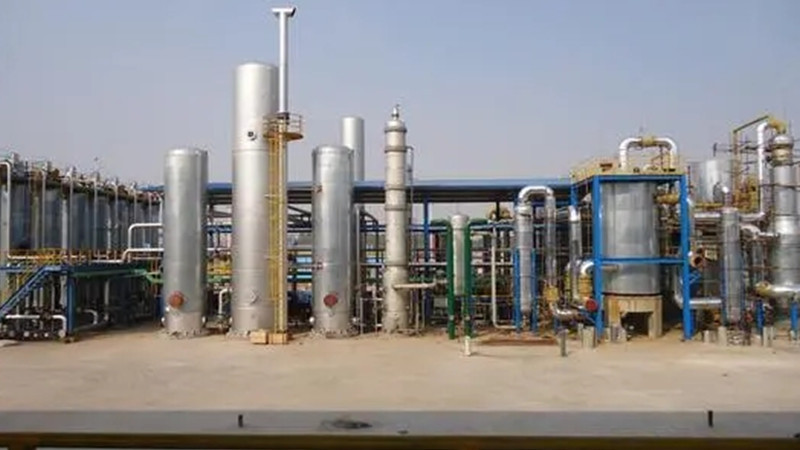
Precautions for Steam Reforming Catalyst Oxidation
Temperature Control: Minimize temperature differentials between furnace tubes to prevent localized overheating.
Passivation Temperature: Limit passivation temperature to below 700°C. Following system shutdown and cooldown, initiate passivation at temperatures between 600 to 650°C for approximately 4 hours, with analysis of non-condensable gases at the reformer outlet.
Catalyst Reduction: Maintain H2O/C ratio between 5 and 7 during catalyst reduction and decrease residence time for H2O/C ratios exceeding 8. Implementing these precautions ensures effective management of steam reforming catalyst oxidation, thereby enhancing catalyst longevity and process efficiency.
Innovation with SYAMCAT Steam Reforming Catalysts
In conclusion, addressing steam reforming catalyst deactivation through proper measures is vital for maintaining optimal performance in industrial processes. Understanding the principles of catalyst deactivation and the impact of water vapor on catalyst activity enables effective management of catalyst oxidation.
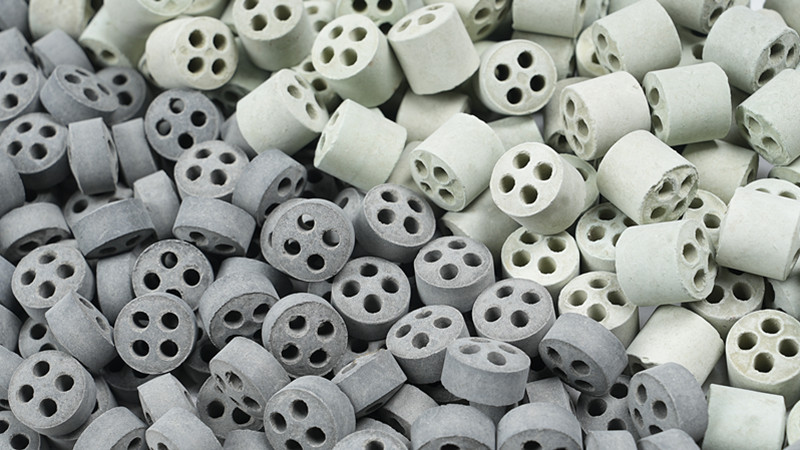
Unlocking Future Opportunities with SYAMCAT Steam Reforming Catalysts
It's also worth highlighting the efficacy of SYAMCAT steam reforming catalyst in mitigating catalyst deactivation and enhancing process efficiency. With its advanced formulation and superior catalytic properties, SYAMCAT offers a reliable solution for steam reforming applications, ensuring prolonged catalyst service life and improved performance.
Contact Us for Your Catalyst Needs
For further inquiries about SYAMCAT steam reforming catalyst or to discuss how it can benefit your specific operations, please feel free to contact us. Our team is dedicated to providing comprehensive support and tailored ammonia solutions to meet your catalyst requirements.
Discover the difference SYAMCAT can make in optimizing your steam reforming processes and achieving your operational goals. We look forward to hearing from you!
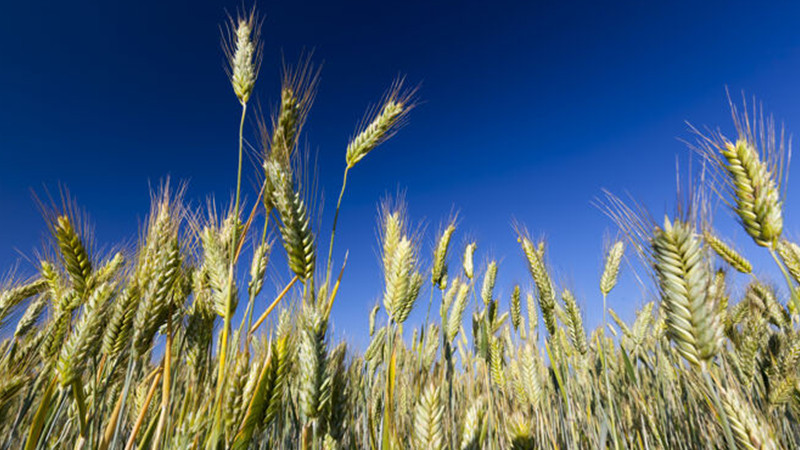