Optimizing Catalyst Particle Size for Enhanced Ammonia Synthesis Efficiency
Optimizing Catalyst Particle Size for Enhanced Ammonia Synthesis Efficiency
Analyzing diffusion efficiency factors and reaction kinetics models for gas-solid catalytic reactions underscores the critical role of catalyst particle size in achieving a high surface utilization rate for ammonia synthesis. The intricate relationship between the reduction process and mass of reduction with the particle size of the ammonia catalyst is evident.
Particle Size and Reduction Process
The reduction process of the catalyst follows a "digging well" pattern, initiating from the surface and progressing inward, inevitably involving diffusion control. This has a direct impact on the rate of catalyst reduction. Furthermore, as water, a byproduct of the reduction, is detrimental to the catalyst, diffusion-controlled reduction increases the residence time of water in the pores, leading to partial reduction of the catalyst and subsequent activity decline.
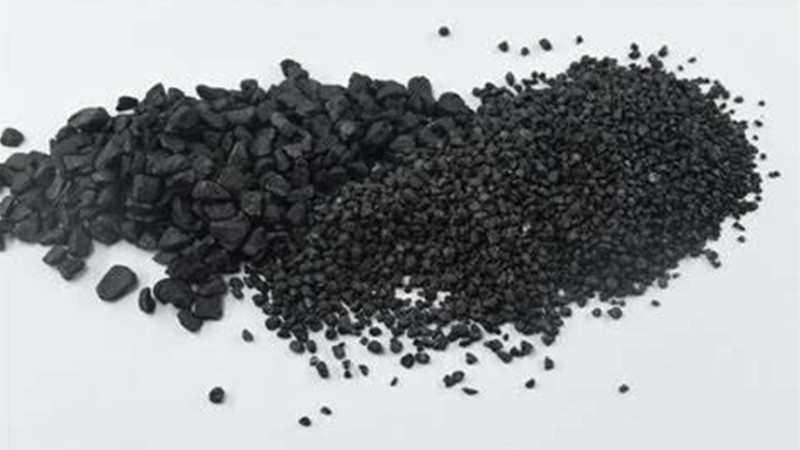
Significance of Particle Size
While smaller catalyst particle sizes are deemed more favorable for enhanced activity, industrial catalyst usage introduces constraints. Smaller particles result in increased bed resistance. The Kozney-Carman equation is employed to express the bed resistance drop (Δp) through the catalyst bed, influenced by particle equivalent diameter (Dp), shape factor (s), resistance coefficient (fm), and void fraction (ε).
Considerations in Particle Size Selection
For a given ammonia synthesis production process and reactor internals, after determining the catalyst model, selecting the ideal ammonia synthesis catalyst particle size distribution becomes crucial to achieve high catalytic activity while minimizing bed resistance. Tables 5 and 6 provide insights into the relationship between particle size, relative activity, relative pressure drop, and common catalyst particle size choices for various tower types.
Table 5: Particle Size, Activity, and Pressure Drop Relationship:
Particle Sizemm
|
Relative Activity(%)
|
Relative Activity(%)
|
1-1.5
|
100
|
100
|
1-3 | 98.4 | 73.5 |
2-4 | 92.9 | 40.8 |
3-6 | 86.7 | 26.0 |
3-9 | 85.2 | 21.9 |
6-9 | 79.7 | 13.9 |
6-12 | 78.1 | 12.2 |
Note: Relative activity and pressure drop vary with different catalyst models.
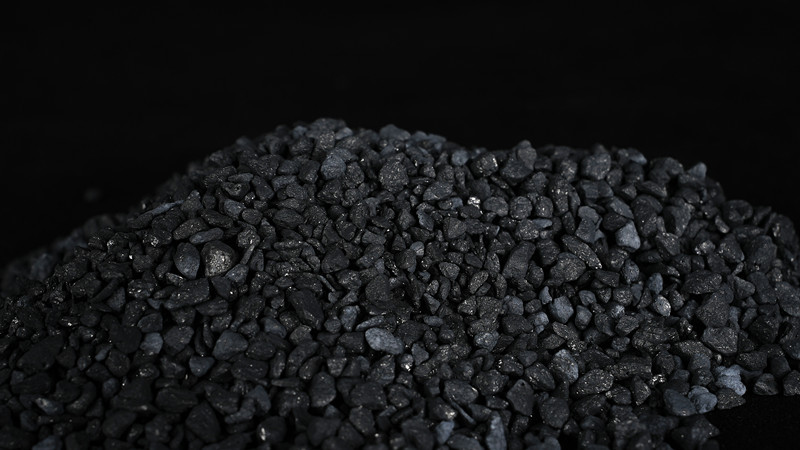
Table 6: Catalyst Particle Size for Different Tower Types:
Tower Type
|
Common Catalyst Particle Size (mm) |
φ500 φ600
|
2.2-3.3,3.3-4.7
|
φ600 φ800 | 3.3-4.7,4.7-6.7 |
φ800 φ1000 | 4.7-6.7,6.7-9.4 |
Large Axial Tower Axial/Radial Tower | 6.0-10.0 |
Axial/Radial Tower | 1.5-3.0 |
Note:
(1) In axial towers, appropriate placement of larger catalyst particles at the bottom and top is recommended during catalyst loading;
(2) Considering catalyst activity and bed pressure drop, the selection of catalyst particle size may involve a combination of two or more sizes.
This study emphasizes the crucial role of catalyst particle size in ammonia synthesis efficiency and provides practical insights for optimizing particle size distribution for enhanced catalytic activity and reduced bed resistance.
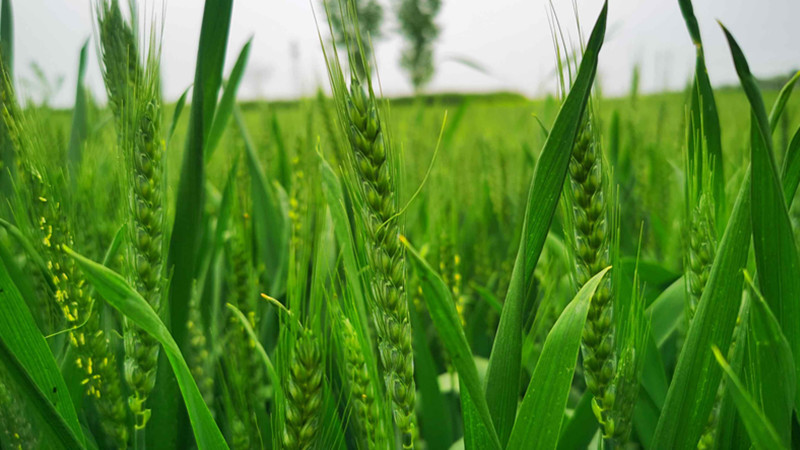
The above briefly introduces “Optimizing Catalyst Particle Size for Enhanced Ammonia Synthesis Efficiency” , If you would like to learn more or are in search of a manufacturer for ammonia synthesis catalysts for your company, please feel free to contact us.
SYAMCAT is a professional manufacturer of ammonia synthesis catalysts with over 30 years of catalyst experience and history. Through continuous technological innovation, we offer catalyst solutions for ammonia production. We are dedicated to assisting ammonia plants and fertilizer manufacturers in optimizing production efficiency while reducing environmental impact. Our aim is to contribute to the sustainability of global agriculture and food security.