SYAMCAT Catalyst Production: Catering to the Growing Needs of Ammonia Plants
SYAMCAT Catalyst Production: Catering to the Growing Needs of Ammonia Plants
In recent times, there has been a significant surge in demand for ammonia synthesis catalysts. SYAMCAT's production department is actively working to meet this escalating demand, focusing on optimizing production processes, implementing stringent quality control measures, efficient packaging methods, and ensuring the secure storage of ammonia catalysts.
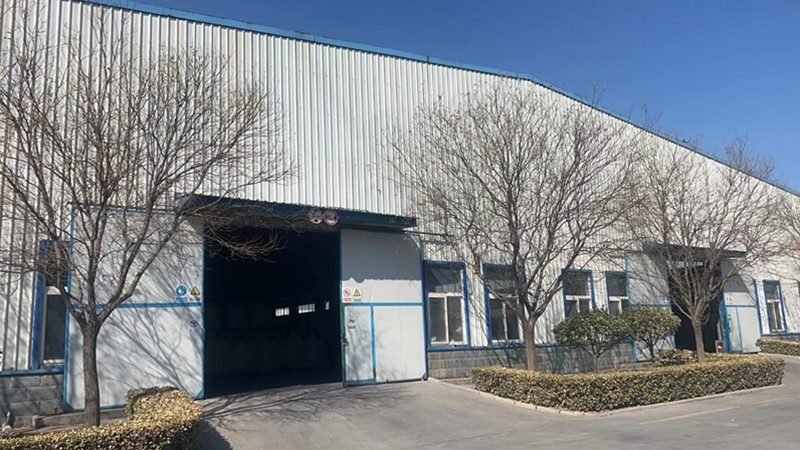
Production process of ammonia synthesis catalysts
SYAMCAT places a high emphasis on the production process of ammonia synthesis catalysts, meticulously controlling every aspect from the selection of raw materials, monitoring of active components, chemical composition balancing, to the overall control of the production process. These processes adhere to strict standards and procedures.
Given that our recent clients have adopted large-scale energy-efficient processes (such as AMV, Braun, LCA), our professional team recommends and configures the use of SYAMCAT A217 and SYAMCAT A217R. This is the second generation of synthetic ammonia catalysts from SYAMCAT, featuring a broad temperature range, high activity, and excellent performance.
The primary component of SYAMCAT A217 ammonia synthesis catalyst is ferric oxide (Fe3O4), supplemented with appropriate amounts of cobalt oxide, alumina, potassium oxide, and calcium oxide as additives. SYAMCAT A217R, an enhancement of SYAMCAT A217, undergoes a pre-reduction process on specialized factory equipment to convert it into active α-Fe. For safety during transportation, storage, and loading, controlled passivation with oxygen is applied to the surface of catalyst particles, including the micro-porous surface. This results in the formation of an FeO film, ensuring not only the safety of the catalyst but also facilitating easy reduction during usage. After pre-reduction, SYAMCAT A217R achieves a reduction degree of over 90%, with oxygen content generally below 2%.
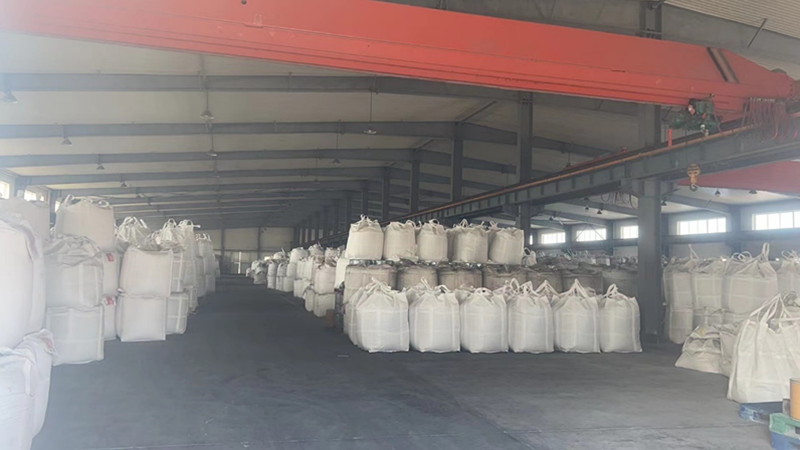
Strict Quality Control by SYAMCAT
SYAMCAT prioritizes stringent quality control measures for its synthetic ammonia catalysts. From the initial stages of raw material selection to the final stages of production, each step undergoes meticulous scrutiny to ensure the highest standards of quality and performance.
The quality control processes at SYAMCAT encompass precise monitoring of raw material selection, careful regulation of active components, and meticulous balancing of chemical compositions. These stringent procedures contribute to the production of synthetic ammonia catalysts that meet or exceed industry benchmarks.
To further guarantee the quality of its products, SYAMCAT employs advanced testing methods and adheres to international quality assurance standards. This commitment to quality control not only ensures the safety and effectiveness of the catalysts but also establishes SYAMCAT as a reliable and trusted provider in the field of ammonia synthesis catalysts.
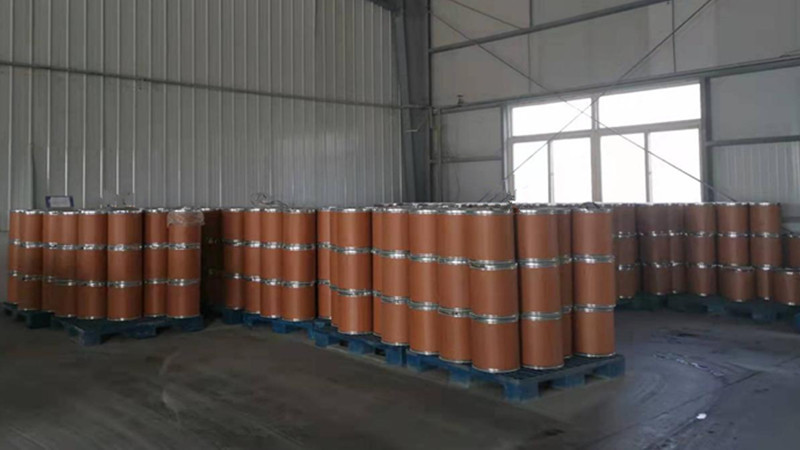
Packaging and Storage Guidelines
SYAMCAT enforces strict packaging and storage measures for ammonia synthesis catalysts.
Ammonia catalysts are sealed in iron drums with plastic liners:
In the reduced state: Net weight of 80 kgs per drum.
In the oxidized state: Net weight of 100 kgs per drum.
Please refrain from opening the drum cover when not in use to prevent contamination.
Storage Guidelines for Ammonia Synthesis Catalysts:
Avoid moisture, and prevent impact or rolling during storage.
Take strict precautions against contamination from oil, dust, and other chemicals.
These measures ensure the quality and effectiveness of SYAMCAT's synthetic ammonia catalysts throughout the packaging, storage, and application processes.
The above briefly introduces “SYAMCAT Catalyst Production: Catering to the Growing Needs of Ammonia Synthesis Plants“ , If you would like to learn more or are in search of a manufacturer for ammonia synthesis catalysts for your company, please feel free to contact us.
SYAMCAT is a professional manufacturer of ammonia synthesis catalysts with over 30 years of catalyst experience and history. Through continuous technological innovation, we offer catalyst solutions for ammonia production. We are dedicated to assisting ammonia plants and fertilizer manufacturers in optimizing production efficiency while reducing environmental impact. Our aim is to contribute to the sustainable development of global agriculture and food security.